Equipment Maintenance Logs
Any business that relies on the use of equipment needs to have their gear running at optimal performance. When equipment is down for maintenance, it slows downs business processes and necessitates higher levels of repair fees. The solution to this problem is preventative maintenance. Preventative maintenance helps keep machines (including fleet vehicles) running as often as possible. The machines are simply less likely to break down if they’re taken care of properly.
Managing all of the preventative maintenance necessary to run a business is where things can get tricky though. That’s why understanding the nuances of equipment maintenance logs is of paramount importance. Equipment maintenance logs can help businesses manage and keep track of all maintenance (including preventative maintenance) to keep their businesses operating at peak performance.
Read on to learn more about equipment maintenance logs, types of maintenance logs, the benefits of using them, and how to make one.
What Are Equipment Maintenance Logs?
Equipment maintenance logs are essential tools in fleet management. They are meticulously detailed records of all service, repairs, and preventative maintenance carried out on a vehicle or piece of equipment. From minor adjustments to major overhauls, each action is documented, typically noting the date of maintenance, specifics of the work conducted, the person who completed the task, any replaced parts, and associated costs.
Why do businesses take the time and energy to keep these logs? The necessity of these logs lies in their ability to serve several indispensable purposes. Firstly, they offer a comprehensive historical account of a fleet’s condition, allowing for effective monitoring of wear and tear.
The business is able to accurately predict potential malfunctions and proactively schedule preventative maintenance and repairs at a convenient time, without halting business. Essentially, this strategic approach not only assures the longevity of the vehicles but also ensures their safe operation, a critical concern in industries where equipment reliability and safety are non-negotiable.
Moreover, equipment maintenance logs are pivotal in regulatory compliance. Many industries are bound by stringent safety regulations that demand regular and systematic maintenance of equipment. A well-kept maintenance log helps adhere to these standards, protecting businesses from unnecessary legal complications and potential reputational damage should a machine break down and fail to meet compliance standards.
Effective fleet management necessitates attention to detail, and equipement maintenance logs help make that simpler. With well-curated equipment maintenance logs, businesses do more than merely keep their fleet running; they optimize performance, assure safety, and enhance overall productivity.
Example of an Equipment Maintenance Log
Ready to get started utilizing equipment maintenance logs? It’s helpful to see what an equipment maintenance log can look like. Here’s what a template could look like for you:
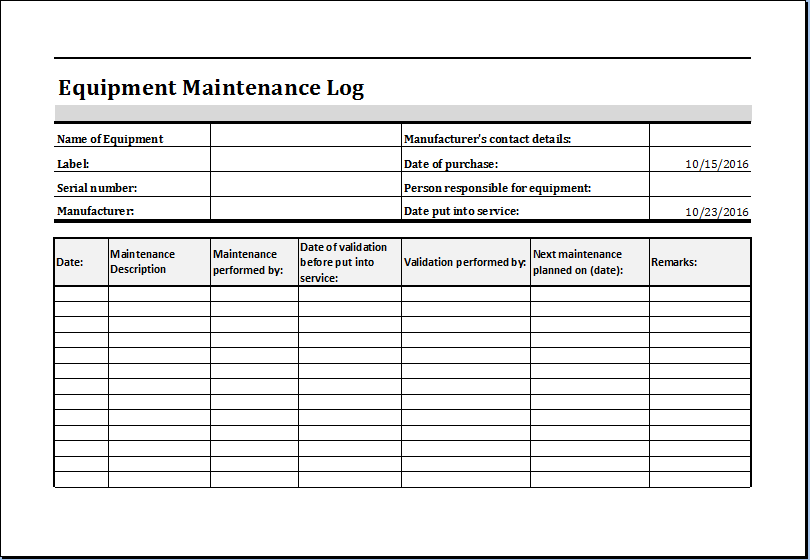
Types of Equipment Maintenance Logs
When something breaks down, it can be a catastrophe. That’s why preventing that is so important. Equipment maintenance logs can come in several different forms. Understanding the types of equipment maintenance logs can greatly enhance the effectiveness of your fleet management. Let’s delve into three specific types of logs: maintenance schedule logs, machinery maintenance logs, and project logs.
Maintenance Schedule Logs
Maintenance schedule logs record all timetables for every project within an organization. In an essence, these logs provide a holistic map of everything happening at the company and where all equipment is needed. For example, if a company has a project requiring the use of a fleet truck, the maintenance schedule log would record the use of that truck for the project.
Why? Maintenance schedule logs serve as a proactive tool for planning and organizing routine maintenance checks on all your vehicles and equipment. If you know that a piece of equipment is going to be used for an upcoming project, you know it may need preventative maintenance before that. You can effectively schedule maintenance knowing exactly when something is needed—that way repairs are done in between projects with the machines prepared for operation by their next needed use.
By effectively using maintenance schedule logs, you ensure your equipment undergoes regular, scheduled maintenance, which can greatly extend the lifespan of your machinery and help avoid unexpected and costly breakdowns.
Machinery Maintenance Logs
Machinery maintenance logs, as the name suggests, focus on individual pieces of equipment. These logs offer an in-depth record of all service, repairs, and maintenance conducted on a specific machine or vehicle. They typically include the dates of each service, the person who performed the task, the type of work carried out, any parts replaced, and the associated costs. These logs are essential for tracking the health and performance of each machine, identifying recurring problems, and forecasting potential issues before they escalate.
Using machinery maintenance logs, you’re able to more accurately predict when a machine may need preventative maintenance because you know exactly what’s been performed on the machine and when its upcoming service needs are. This log will help you keep track of every needed oil change for trucks, as well as the larger repairs.
Project Logs
Project logs offer a broader view by focusing on the particular projects or operations within your business. These logs can include maintenance schedule logs and logs from other departments. These logs track how all the machinery and equipment are used, their maintenance schedules, any breakdowns, and repairs during the project’s lifespan.
By providing a project-specific overview of equipment usage and maintenance, these logs can aid in improving future project planning and execution. They can help identify patterns, such as specific machines requiring frequent repairs during certain types of projects, and provide valuable insights to enhance efficiency and reduce downtime.
Each of these logs plays a vital role in efficient fleet management, providing a different lens through which to view and manage your equipment maintenance. When used collectively, they form a comprehensive system that ensures the longevity of your fleet, optimizes operational efficiency, and promotes regulatory compliance.
What Are the Benefits of Equipment Maintenance Logs?
The use of equipment maintenance logs carries far-reaching benefits that enhance various facets of operating a business that relies on equipment. Here are several of the key benefits equipment maintenance logs provide:
Ease of Scheduling Preventative Maintenance Work
Equipment maintenance logs provide a detailed history of each piece of machinery’s past service and repairs—and each piece of equipment’s use in projects. This information makes it easier to schedule regular preventative maintenance, reducing the risk of unexpected breakdowns and extending the lifespan of your equipment. You will know when every machine is needed and can schedule maintenance around use while ensuring that every machine is properly taken care of.
Faster Failure Diagnosing and Repair Process
With a comprehensive log, technicians can quickly identify patterns of recurring issues, accelerating the diagnosis of failures. This saves significant time during the repair process and decreases the duration of unplanned downtime.
Creates More Cost-Effective Decisions
Maintenance logs allow managers to track the cost of repairs and maintenance for each piece of equipment. That can actually reduce costs. This data aids in making informed decisions, such as whether to continue repairing an aging machine or replace it, ultimately leading to more cost-effective decisions. The logs provide you with the information you need to make the best decisions for your equipment.
Increase Equipment Resale Value
Well-maintained equipment invariably fetches a higher resale value. Detailed maintenance logs can serve as proof of regular servicing and proper care, enhancing the perceived (and actual) value of the machinery. If you’re taking care of your machines, you’ll be able to sell them later for more.
Reduced Inventory and Operation Costs
Maintenance logs can help identify parts that frequently need replacement, allowing for more strategic inventory management. This can reduce costs associated with excessive inventory and minimize operational delays due to unavailability of parts.
In addition, major repairs from breakdowns simply cost more than preventative maintenance, so it saves companies money in the long run to spend a little on preventative maintenance at a time to save from having to make full blown replacements.
Improve Workplace Safety
Regularly maintained equipment is safer to operate. By adhering to the maintenance schedules outlined in the logs, businesses can minimize the risk of accidents caused by equipment failure, thereby improving workplace safety.
Enhance Accountability
With a detailed log, it’s clear who performed what maintenance task and when. This promotes responsibility and accountability among the maintenance team and ensures a high standard of work.
In summary, the implementation of equipment maintenance logs significantly bolsters operational efficiency, safety, accountability, and financial management within a fleet operation. The return on investment in this systematic approach to equipment care is indeed substantial.
How to Make an Equipment Maintenance Log
Crafting a comprehensive equipment maintenance log is a straightforward process, but it requires attention to detail. Here’s a step-by-step guide on how to create an effective equipment maintenance log, including essential information you should include:
Name of the Asset: Start by listing the name of the equipment or vehicle. This helps to easily identify and categorize each asset in your fleet.
Serial Number: Next, note the unique serial number or identification number of the equipment. This allows for accurate tracking of each individual piece of equipment.
Equipment Manufacturer and Contact Details: Provide the name of the equipment’s manufacturer along with their contact details. This can be invaluable for seeking advice, ordering parts, or addressing warranty issues.
Date of Purchase: Log the date the equipment was purchased. This helps in tracking the equipment’s age, which is crucial for planning maintenance schedules and anticipating end-of-life replacement. If a machine is bought used, it’s helpful to note both when you purchased it and the year it was made.
Date of First Use: Note the date when the equipment was first put into operation. This provides further insight into the machine’s usage history.
Operator Responsible for the Asset: Include the name of the operator or person responsible for the asset. This promotes accountability and allows for more efficient communication if any issues arise. The operator might be the driver of a fleet vehicle or the employee who uses a particular forklift.
Location of Facility: Document the facility or site where the equipment is primarily located. For businesses with multiple sites, this assists in monitoring and managing equipment across different locations.
Date of Maintenance: Record the date of each maintenance task. This will aid in scheduling future preventative maintenance and help track the frequency of services and repairs.
In creating an equipment maintenance log, consider using a consistent format across all entries for easy comparison and analysis. This could be a physical logbook, a spreadsheet, or a specialized maintenance software program, depending on your business’s size and needs. Regular updates to the log are crucial, ensuring that all information remains current and accurate.
Because of the importance of regularly updated logs, you might consider using an online log or a logging tool that can be easily synchronized across your organization quickly and accurately.
Summit Fleet
A well-maintained equipment log serves as an invaluable tool for fleet management, offering a clear picture of your assets’ health, aiding in strategic decision-making, and contributing to the overall efficiency and safety of your operations. It’s a tool that helps you keep track of the ins and outs of your machines.
If you’d rather not spend the time creating and updated machine logs, renting fleet vehicles might be right for you. When you rent from Summit Fleet, you can be sure that you’re getting well-maintained vehicles that are taken care of. Our team utilizes equipment maintenance logs to ensure that every vehicle is maintained and operating in prime condition.
Want to learn more about how Summit Fleet can help you focus on your bottom line? Find out here!