Management of Equipment
Every business has a myriad of assets that help the company run properly and efficiently. From technology like laptops and cameras to big-scale vehicles and machines, tracking and overseeing the use of such equipment is a big task. It’s best to create an equipment management system that helps your company fully utilize and protect its assets and equipment. Here’s what we recommend!
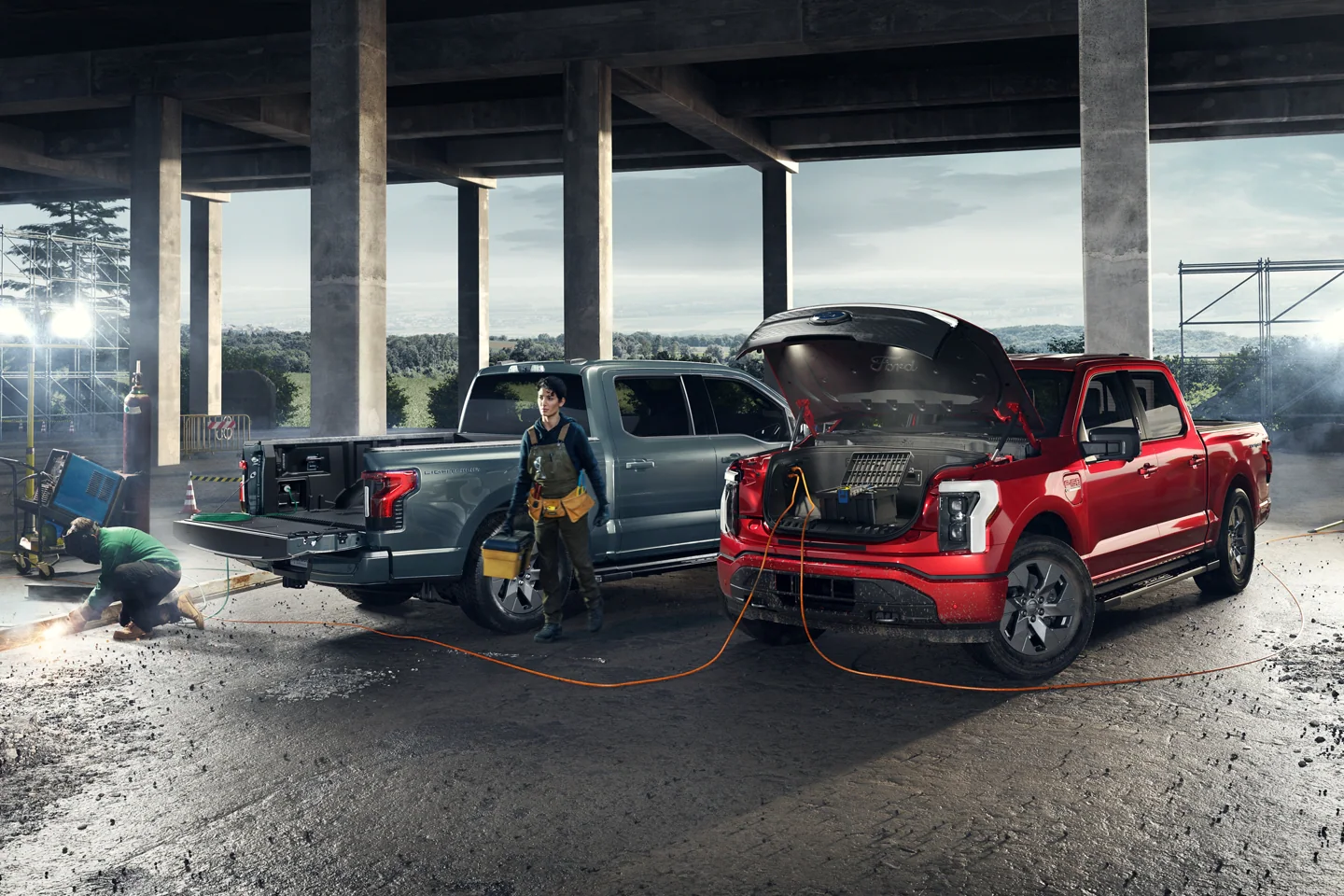
What is Equipment Management?
Equipment management is the process of efficiently overseeing and controlling the lifecycle of equipment within an organization. It involves tasks like asset acquisition, utilization, maintenance, and tracking; it also includes when and how equipment is disposed of to ensure optimal performance, minimize downtime, and maximize return on investment.
Equipment management tends to fall into an administrative role as well as a maintenance one because it’s such a multifaceted responsibility. With elements like IoT, telematics, and device fleets, most industries are relying on the real-time visibility and convenience of these assets. In response, effective management of equipment is so crucial in 2023 as assets become more sophisticated and essential to your operations.
Equipment management is great for productivity and efficiency, too, especially because it helps companies understand how their equipment is being used and gain insights into overall equipment costs. Essentially, if you want your organization to properly handle its equipment and spending so that it’s effective, you need an equipment management system in place.
What Can Fleet Managers Track with Equipment Management Systems?
One of the easiest ways to take care of your assets is to use software like equipment management systems, and this is even more important for fleet managers. Not only do they simplify tracking your equipment and vehicles, but they also generate useful insights and data about both the assets and your operations.
Some of the primary functions of this kind of system include:
Equipment Management Best Practices
Let’s get down to brass tacks here: what do you need to do to have a strong equipment management system in place? Here are the essentials to work into your company’s operations.
How Summit Fleet Can Help
Asset, inventory, and equipment management is no small feat, which you have to consider as you build a fleet of vehicles and equipment. It’s not just their upfront cost you must consider—it’s also their maintenance and management, too.
Renting a fleet makes equipment management that much easier since you don’t need to worry about fleet maintenance, registration, licensing, or other incidental fees. Summit Fleet offers various truck rental options no matter what industry; whatever your needs are, we have a truck rental for you.
Ready to get started? Get your rate from Summit Fleet today.